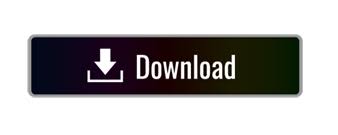
The impression on the ware would then be taken onto thin paper and engraved onto glazed earthenware.

This technique involved the use of oil, where it would be poured on the ware/plate and the excess wiped off. This technique was developed in the eighteenth century and entailed two main methods: overglazing and underglaze. Since different pigments fuse at varying temperatures, it would take more than just a few firings to fuse all of them, which could be pretty pricey at times. Then, the potter would fire the ware, so the enamel fuses to the ware. It involves painting overglaze on the ware using pigments attained from colored glass that is finely powdered. The technique was adopted from the original porcelain industry. That said, the decorative techniques that potters would use include the following: Enameling One of the most used techniques was painting overglaze on the ware using pigments from fine-colored glass and firing for it to stick to the ware. Potters borrowed techniques from the early porcelain industry. What is Creamware Used For?Įarly on, in the mid-eighteenth century, creamware was primarily used for decoration. It may help you spot the difference between your vintage ceramics. I’ve written an entire article about the differences and similarities between pearlware and creamware. Instead of being cream, most pearlware has a blueish tint to it.Įven so, it takes time and practice to be good at identifying and differentiating various earthenware. Pearlware: It is the more desirable form of creamware that Josiah Wedgwood developed in 1779. Whiteware is in the ceramic in the plates you will find in stores today. Whiteware: As per the name, this earthenware is immaculately white. It also exudes a creamy look, almost like light butter. The following are ways through which you can identify creamware in comparison to other types of earthenware:Ĭreamware: Creamware stands out because of its cream color. Generally, though, earthenware is relatively thicker and heavier than other forms of pottery.įurthermore, earthenware has a general rustic feel and look. This is because different types of earthenware come in different colors. The easiest way to identify earthenware is through color. Thus, the Factory of Leeds became a key player in the manufacture of creamware. As a result, major pottery factories of the time, more so factories in Leeds, took up creamware as the primary craft.
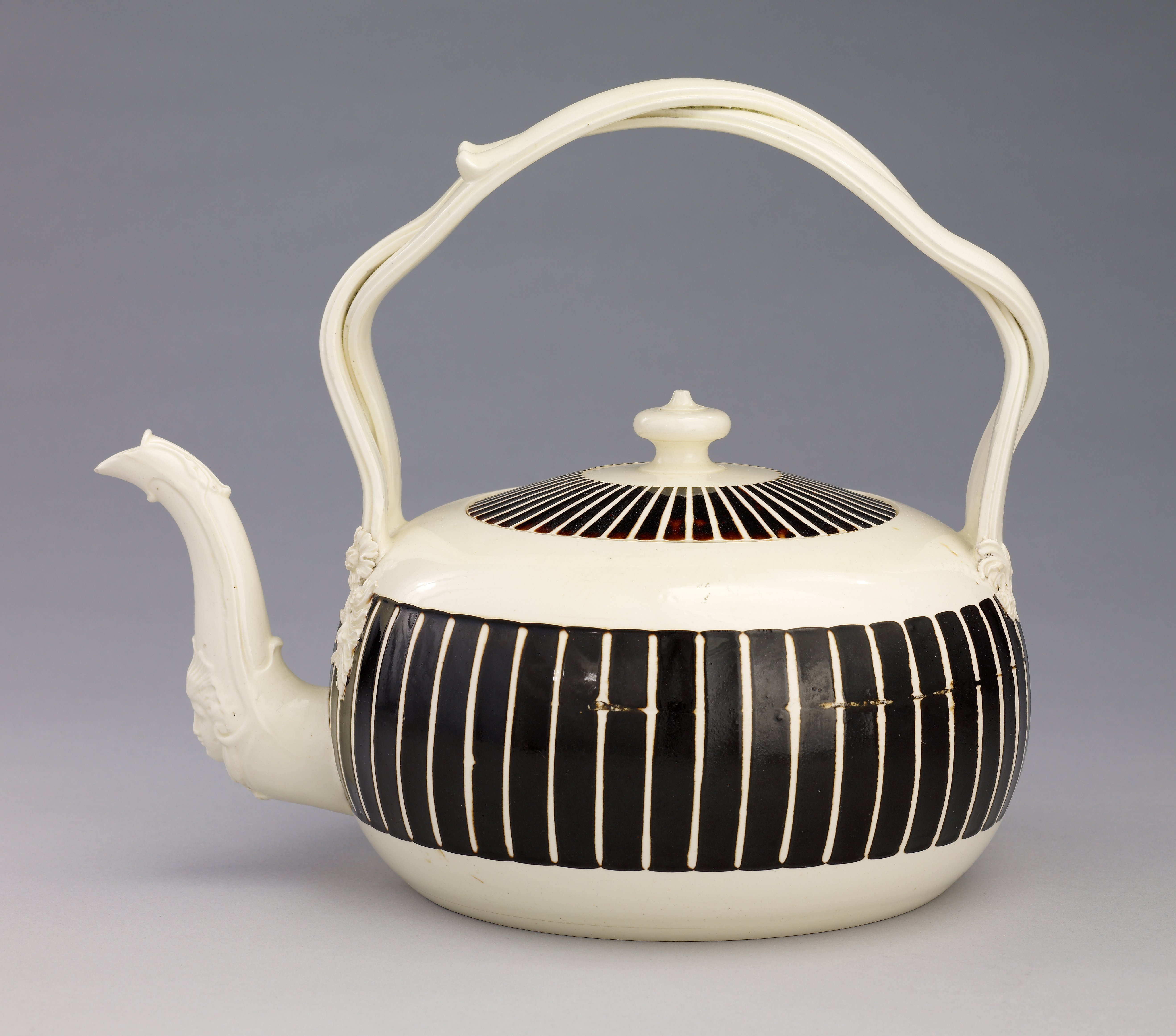
The success of creamware led to the demise of pewter vessels and tin-glazed earthenware. Not only was creamware used all over Europe, but it was also popular in the East Indies, West Indies, and various American countries. The increased demand for creamware in England and other countries of the world led to immense commercial success in the industry. Queen’s Ware, Image by VAwebteam at English Wikipedia, As per the name, tortoiseshell ware is earthenware that is decorated with a dark palette to imitate a tortoise’s shell. He was the skill and talent behind whieldon ware, otherwise referred to as tortoiseshell ware. One of the most recognizable pioneer creamware potters was Thomas Whieldon. The glazed mixture would then be fired one more time. As per this method, the ware would first be fired into a biscuit state, after which it would be glazed. In the 1740s, the Staffordshire potters came up with another method of developing creamware where ingredients would be mixed and ground in water to form a fluid glaze. So, the crafters had to change tactics, if only for their health. This method proved to be problematic as the lead mixture would poison the potters, and the process of grinding flintstones would result in the potter’s rot disease. The mixture would be dusted on the ware before being fired only once. Originally, creamware was made by mixing lead powder of galena with calcined flint. If you are interested in salt-glazed pottery, you might like to check out a post I wrote about salt-glazing here.
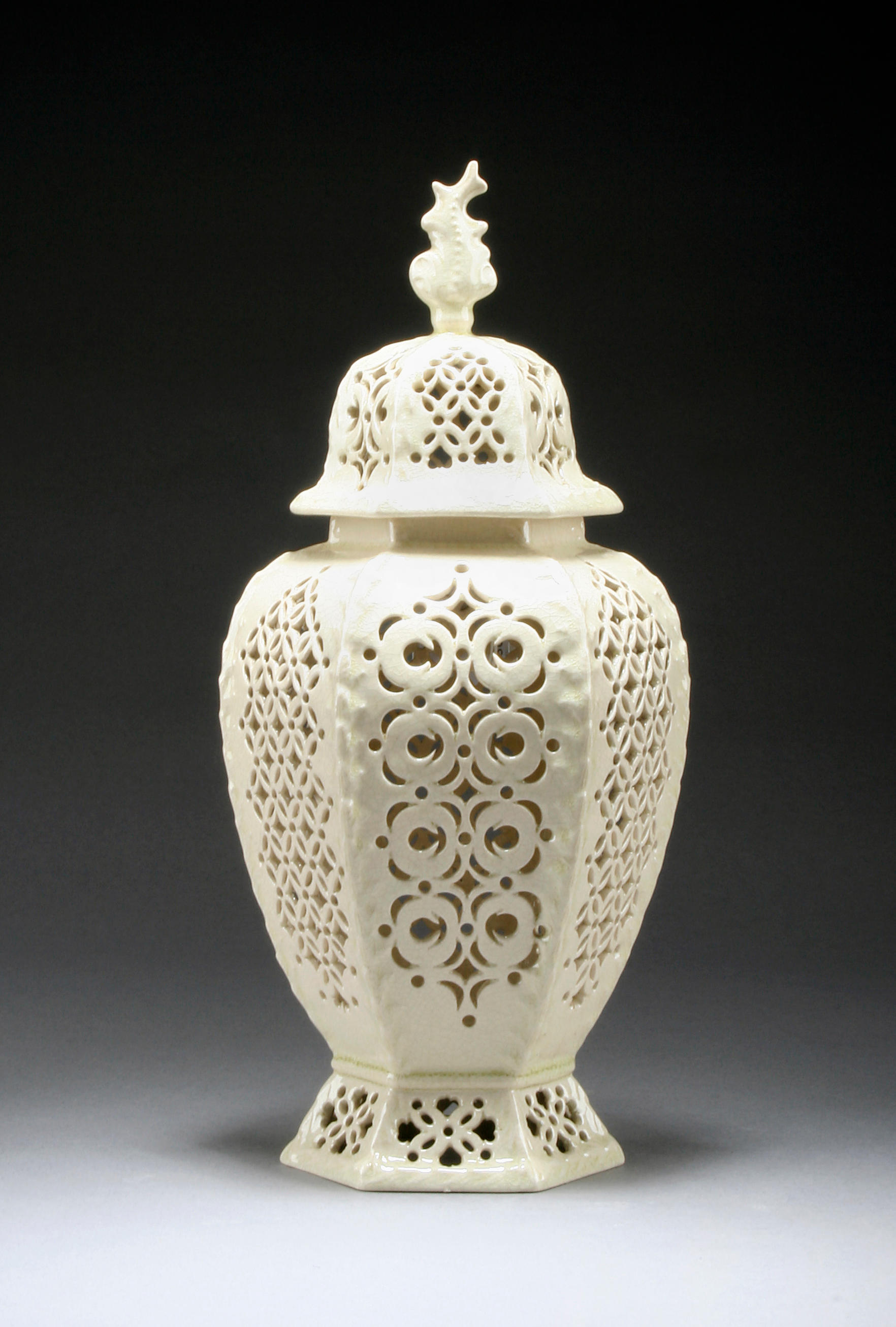
Salt-glazed stoneware is fired at temperatures between 10C. Note that creamware is made in much the same way as salt-glazed stoneware, with the primary difference being that the firing process of creamware is done at a lower temperature.

It is then glazed with lead to create cream-colored earthenware. Via Wikimedia Commons How Creamware Pottery is DevelopedĮssentially, as we have already seen, creamware is the result of combining white clay and calcined flint and firing it at a temperature of about 800C ( source). Leeds Creamware Dish, Image by Rijksmuseum, CC0,
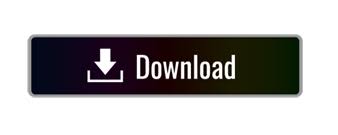